运转过程中发作电机差错计数器溢出过错。
对策:增大差错计数器溢出水平设定值;减慢旋转速度;延长加减速时间;负载过重,需求从头选定更大容量的电机或减轻负载,加装减速机等传动组织提高负载才能。
第六类故障主要是电源、地线和信号线的噪声(干扰)问题的解决或改善主要在于工程设计时的经验和日常维护中的观察分析。
要减小故障率,很重要的一点是要重视工厂工艺和安全操作规程,在日常的工作中要遵守工艺和安全操作规程,严格执行—些相关的规定,如保持集中控制室的环境等等,同时在生产中也应加强这些方面的管理。
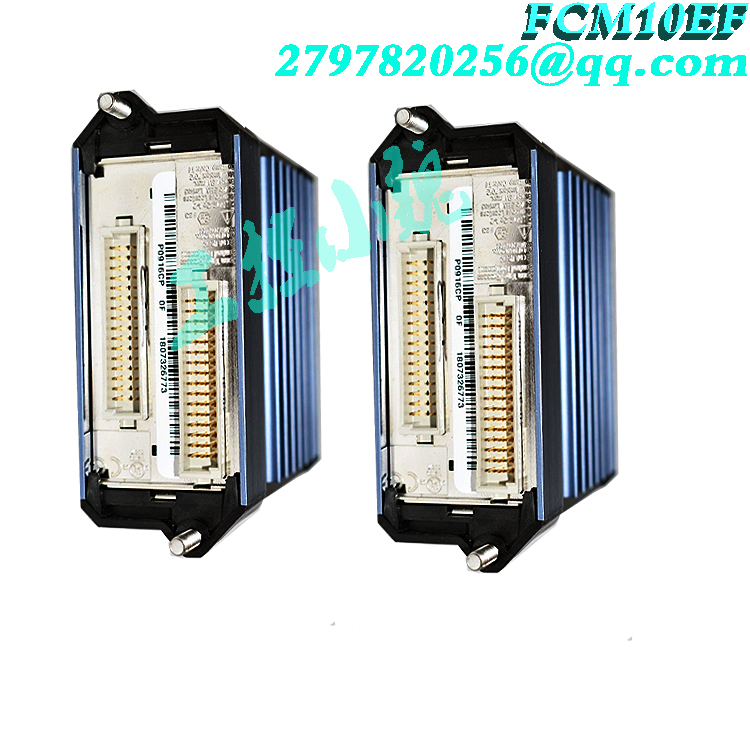
过程控制系统本身是一个完整的系统,所以在分析故障或处理故障时也要注意系统性,单独的对某一部分的优化有时并不能提高系统的整体性能。如过分追求元器件的精度而不考虑实际的需要以及和相关设备精度的匹配,将徒然增加系统成本。在日常维护中也有过把系统越改越复杂的现象,如采用复杂的控制方式和设备来实现本可以用简单装置来实现的控制,违背了经济、简单、实用的原则,并可能会增加故障率,这也是要注意的地方。
In the whole PLC control system, the site is the most prone to failure, and the site is the most prone to failure in the following aspects.
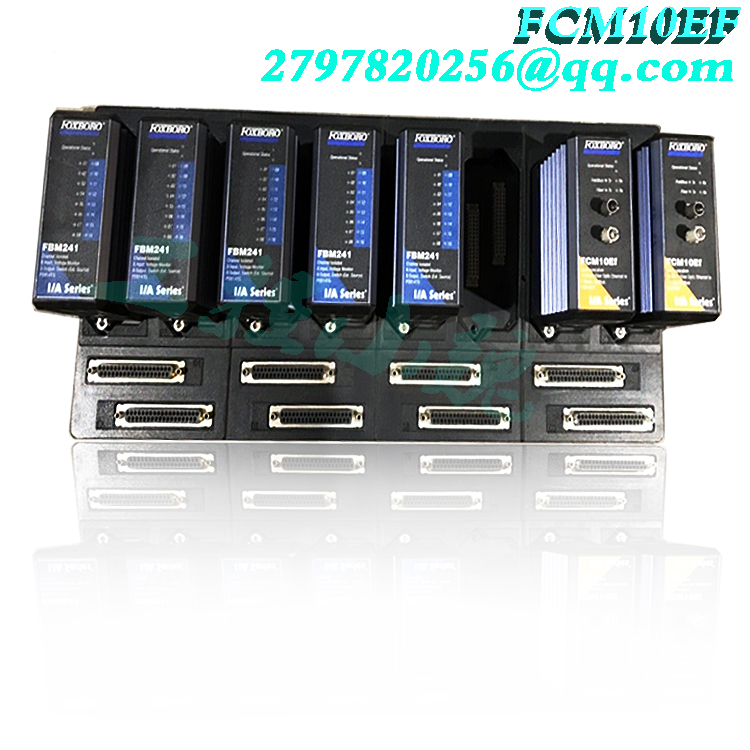
1. The first type of fault point is also the most fault point) in relays and contactors
For example, in the daily maintenance of the PLC control system of a production line, the largest consumption of electrical spare parts is various relays or air switches. In addition to the quality of the product itself, the main reason is that the site environment is relatively bad. For example, the contacts of contactors exposed to the production environment are easy to ignite or oxidize, and gradually heat and deform until they cannot be used. All on-site control boxes of the production line are made of panels and cabinets with good tightness, and the service life of its internal components is significantly longer than that of other open panels and cabinets. Therefore, to avoid such failures, high-performance relays should be selected as far as possible, and the use environment of components should be improved to reduce the frequency of replacement and reduce the impact on system operation.
2. The second type of fault frequently occurs on equipment such as valves or rams
Because the relative displacement of the actuator of such equipment is relatively large; Or the transmission structure is complex, and if the mechanical, electrical, hydraulic and other links are not in place, errors or faults will occur. Under long-term operation, if there is no operation and maintenance, it is easy to cause jamming, blocking and leakage of valve body parts. Therefore, when the system is running, it is necessary to strengthen the patrol inspection of such equipment and timely handle the problems found. Our factory has established a strict point inspection system for such equipment, regularly checking whether the valve is deformed, whether the actuator is flexible and available, and whether the controller is effective, which well ensures the effectiveness of the entire control system.
3. The third type of fault point may occur on some elements or equipment in switch, limit position, safety protection and field operation
The reason may be due to long-term wear, or corrosion and aging due to long-term use. For example, the distribution cart on the kiln tail ball storage of the production line moves frequently, and the dust on the site is large, so the contact of the proximity switch is deformed, oxidized, and blocked by dust, resulting in poor contact of the contact or insensitive action of the mechanism. The treatment of this kind of equipment failure is mainly reflected in regular maintenance to keep the equipment in good condition at all times. For limit switches, especially those on heavy equipment, in addition to regular maintenance, multiple protection measures should be added in the design process.
4. The fourth kind of fault point may occur in the sub-equipment of PLC system
Such equipment as junction box, wire terminal, bolt and nut, etc. The causes of such failures are not only related to the manufacturing process of the equipment itself, but also related to the installation process. For example, some people think that the tighter the wire and screw connection is, the better, but it is easy to cause difficulties in disassembly during secondary maintenance, and it is easy to cause damage to the connector and its nearby components during heavy disassembly. Long-term sparking and corrosion are also the causes of the failure. According to engineering experience, such failures are generally difficult to find and repair. Therefore, the installation and maintenance of the equipment must be carried out according to the installation process required by the installation, without leaving any hidden danger of the equipment.
5. The fifth type of fault points are sensors and instruments
This kind of fault is generally reflected in the abnormal signal in the control system. When installing this kind of equipment, the shielding layer of the signal line should be reliably grounded at one end, and should be laid separately from the power cable as far as possible, especially the frequency converter output cable with high interference, and software filtering should be carried out inside the PIC. The discovery and handling of such failures are also related to routine patrol inspection. Problems found shall be handled in time.
6. The sixth type of fault is mainly the noise (interference) of power supply, ground wire and signal wire
The solution or improvement of the problem mainly depends on the experience in engineering design and observation and analysis in daily maintenance.
In order to reduce the failure rate, it is very important to pay attention to the process and safety operation procedures of the factory, abide by the process and safety operation procedures in daily work, strictly implement some relevant regulations, such as maintaining the environment of the centralized control room, etc., and strengthen the management of these aspects in production.
The process control system itself is a complete system, so it is also necessary to pay attention to the systematicness when analyzing or dealing with faults. The optimization of a certain part alone sometimes cannot improve the overall performance of the system. If the precision of components is excessively pursued without considering the actual needs and matching with the precision of relevant equipment, the system cost will be increased in vain. In daily maintenance, there has also been the phenomenon of changing the system more and more complex. For example, using complex control methods and equipment to achieve the control that could be achieved with simple devices violates the principles of economy, simplicity and practicality, and may increase the failure rate. This is also the place to be noted.
Description
The 60M100 Condition Monitoring System continuouslymonitors wind turbine machine trains using sophisticatedsignal processing algorithms and machine operating states.The 60M100 Monitoring System, as a part of condition- based
maintenance, detects defects months in advance of apotential failure.Depending on the size of your wind farm, early detection canreduce outages and production loss, saving you hundreds ofthousands to millions of dollars per year in lost revenue. Withthe advanced knowledge provided by the 60M100, you canschedule maintenance outages and crane operations inadvance, reducing maintenance costs.The 60M100 Monitor can be used in several configurations:As an independent, standalone condition monitoringsystem.A networked, distributed collection of an integrated part of a machine OEM's control andinstrumentation package.The 60M100 monitor includes features and advantages notprovided in other systems. The monitor systems have allfunctionality required for condition monitoring of windturbine machine trains including signal conditioning,alarming, configuration, speed inputs, and control systemcommunication.
The system components include: 60M100 Monitor, Adapt.windsoftware, Transducers and cables.Sophisticated signal processing algorithms extract dozens of
measurements and health indices from each accelerometerpoint and can be custom tuned to specific bearing and gear
box characteristics.The 60M100 monitors 150 static variablesproducing high resolution waveform data andtrendllines.The 60M100 is a powerful and versatileCondition Monitoring system that providesbasic monitoring functions and advancedsignal processing and rules in a compact,robust unit. The module conditions the inputsignals to make various measurements andcompares the conditioned signals with user-programmable alarms.
Capable of taking input from different sensortypes, the 60M100 System can support up to 12dynamic channel inputs, two Keyphasorsignals, and digital communications. Channel 1through channel 10 interface with 2: -wire ICPtype accelerometers. Channels 11 and 12 can beconfigured to interface with either 2-wire ICPtype transducers or 3-wire proximity probes.Each dynamic channel can be independentlyconfigured with flexible signal processing
options. The Keyphasor channels interface toeither 3-wire proximity probes or other speedsensors which are powered externally.The module provides enhanced capability formonitoring rolling element bearing machinery
and gearing through its 24 bit Analog/Digital .conversion and 40 kHz bandwidth design.The 60M100 System is not a substitute for hardwired safety systems, nor does it replace thestandard systems for the acquisition ofoperational data of the wind turbine.60M100 OverviewThe 60M100 Condition Monitoring System isspecifically designed for continuouspermanent monitoring of wind turbinegenerator machine trains. It is designed tomonitor equipment that requires extremelyhigh reliability and availbility.The 60M100 System is designed to monitoressential characteristics and components of awind turbine, including:Tower swayMain bearingMain rotorGear boxes。All internal bearings2 All bear meshes。Debris monitoringGenerator bearings
Generator groundingIf you need assistance configuring yourmonitoring solution, contact your local BentlyNevada sales professional or Bently .Digital CommunicationsThe 60M100 System includes digitalcommunication capabilities for connection toADAPT software using proprietary protocols viaEthernet connections. The 60M100 systemtransmits data via Ethernet TCP/IP. You canmonitor values and statusyour process and control and other
automation systems.provides extensive communication capabilitiesof all monitored values and statuses forintegration with process control and otherautomation systems using Ethernet TCP/IPcommunications capabilities. It permitsEthernet communications with other 60M100systems and System_ Software. Supported
描述
60M100状态监测系统使用复杂的信号处理算法和机器运行状态持续监测风力涡轮机机组
根据风电场的规模,早期检测可以减少停机和生产损失,每年为您节省数十万至数百万美元的收入损失。借助60M100提供的先进知识,您可以提前安排维护停机和起重机操作,从而降低维护成本。60M100监视器可用于多种配置:作为一个独立的状态监测系统,操作间系统的分布式集合。作为机器OEM控制和仪表包的一个集成部分。60M100监视器包括其他系统没有的功能和优势。监控系统具有风力涡轮机机组状态监控所需的所有功能,包括信号调节、报警、配置、速度输入和控制系统通信。
系统组件包括:60M100监视器、适配器、风机软件、传感器和电缆
每个加速度计点的测量值和健康指数,可根据特定的轴承和齿轮进行定制
60M100监测150个静态变量,产生高分辨率波形数据和趋势。60M100是一个功能强大的通用状态监测系统,在一个紧凑、坚固的单元中提供基本的监测功能和先进的信号处理和规则。模块调节输入信号以进行各种测量,并将调节信号与用户可编程报警进行比较。
60M100系统能够接收不同传感器类型的输入,多可支持12个动态信道输入、两个键相信号和数字通信。通道1至通道10与2线ICP型加速计接口。通道11和12可配置为与2线ICP型传感器或3线接近探头接口。每个动态通道可独立配置为灵活的信号处理
选项。键相器通道与外部供电的三线接近探头或其他速度传感器连接。该模块提供了监控滚动元件轴承机械的增强功能
60M100系统不是硬接线安全系统的替代品,60M100概述60M100状态监测系统专门设计用于持续监测风力发电机组。60M100系统旨在监控需要极高可靠性和可用性的设备。该系统旨在监控风力涡轮机的重要特性和部件,包括:风塔摆动主轴承主转子齿轮箱所有内部轴承2所有轴承啮合碎屑监测发电机轴承
发电机接地如果您需要配置监控解决方案的帮助,请联系您当地的BentleNevada销售专业人员或Bently 。数字通信60M100系统包括数字通信功能,可通过以太网连接使用专有协议连接到ADAPT软件。60M100系统通过以太网TCP/IP传输数据。您可以监控流程和控制的值和状态以及其他
自动化系统。使用以太网TCP/IP通信功能,提供与过程控制和其他自动化系统集成的所有监控值和状态的广泛通信功能。它允许与其他60M100系统和System_ Software进行以太网通信。支持